Unique Solutions From High Shear Dry Extruders
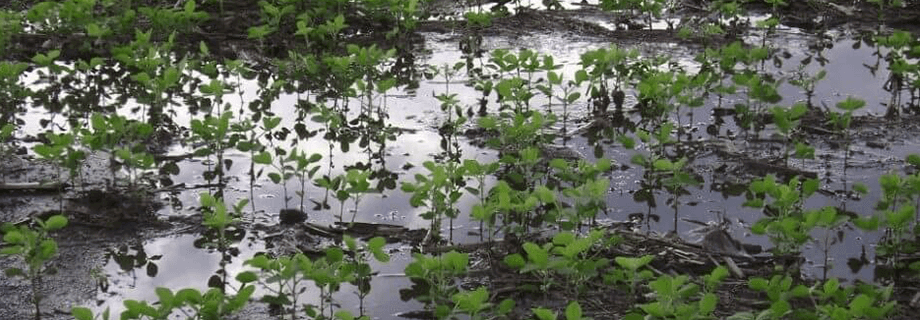
The high shear dry extruder can solve many local problems in a unique way. Here is a great example. On a recent trip to Myanmar in Southeast Asia, I spoke to a group involved with agricultural development. They conduct much of their work in Shan State with soybean production.
As we were talking, I was shocked to learn two things:
- Many of the soybeans, which are exclusively rain-fed in this region, have excessively high moisture contents – as high as 28% at harvest!
- As farmers in this region don’t have an adequate (or often, any) method to dry beans, about 40% rot before they can be used for anything (feeding, seed for next growing season, etc.).
This development group was looking into approaches that could help with this situation, including an inexpensive, low-capacity dryer, as well as using soybean varieties that can remain in the field longer and dry there during less-rainy times.
Insta-Pro Intl has long advocated and worked to develop technologies related to extrusion of potentially valuable co-products that otherwise would go to waste (see here, here, and here). Often, this involves blending two or more ingredients to make the extrusion process possible.
In this situation in Myanmar, a mixture of rice bran (a valuable but unstable co-product of the rice milling industry) and wet beans may work very well. Taking the 28% moisture beans, a mixture of 60% rice bran and 40% wet beans could look something like this example:
Nutrient (%, as-is basis) | Before Extrusion | After Extrusion |
Dry matter | 84 | 89 |
Crude protein | 20.5 | 21.7 |
Crude fat | 15.8 | 16.8 |
Crude fiber | 6.8 | 7.2 |
Total lysine | 1.16 | 1.22 |
Total methionine | 0.36 | 0.39 |
Total threonine | 0.80 | 0.85 |
Total tryptophan | 0.34 | 0.36 |
Table 1: 60% rice bran: 40% wet (28% moisture) soybeans, for example purposes only.
Note that this blend should hopefully result in a low-enough moisture level (11%) after extrusion to allow for long-term storage without the need for an expensive dryer (more on drying here). Only a meal cooler would be required.
This ingredient would work into nearly any type of animal diet, with notable protein and amino acids, and ample fat for energy – all the while with manageable fiber levels.
Rather than throwing away 40% of a soybean crop, utilize technologies, such as co-blending and dry extrusion, that can preserve, and allow utilization of, these materials.
If you see a challenge in your market where product of value is being wasted, we may have a creative solution for you. Our experienced team can work with you to evaluate a potentially profitable solution utilizing high shear dry extrusion technology.