Which Cooler is Right For You? Part 2
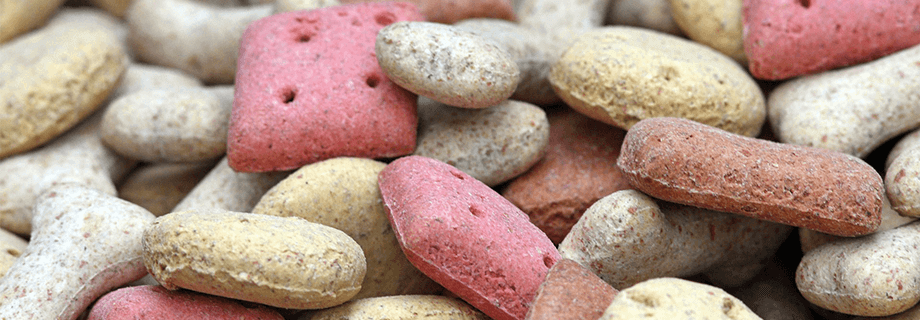
In part 1 of this series on coolers, we discussed the use of rotary drum and counterflow coolers when cooling extruded and/or pressed oilseeds. In Part 2, we will discuss shaped and high moisture products that require moisture elimination and how to properly use a dryer/cooler for this specific application.
The reason for a dryer/cooler is to prepare the product for packaging. Packaging a high moisture product would cause mold to form and increase the risk of rancidity, hence the need for drying. In order to dry a product, heat must be used. This drives out the moisture, but elevates the product temperature. If this heated product were packaged, it would cause condensation inside the package. For this reason, a cooling step is required. The following details how a combination dryer/cooler operates.
Figure 1. Single-pass dryer/cooler (Image courtesy of Norris Thermal Technologies)
Figure 2. Multi-pass dryer/cooler (Image courtesy of Norris Thermal Technologies)
The horizontal belt-style dryer/cooler is used for most shaped and high moisture products. These products usually require high moisture content in order to properly shape and cook. Typical values can be between 18-30% depending on the product. These can be things like textured soy, fish/pet food, and extruded by-products.
Dryer/coolers can be either single or multi-pass, as seen in figures 1 and 2. This varies based on the product properties and moisture content. A large, slow moving belt carries product down the dryer/cooler while ambient air is drawn into the vessel. As it enters, it passes over a heating area which can be either steam or gas fired. This heats up the air which is used for the drying phase. This can be seen by the red arrows in the figures. This heated air is drawn up through the product and exits via an exhaust port to a fan and cyclone.
The cooling portion occurs further down the product stream. Typically, the first part of the dryer/cooler is for drying and the back end cools. The figures show blue lines to represent ambient cooling air being pulled through the product. Some designs allow this air to be recycled and then heated to improve machine efficiency. Finally, product exits the machine for either further processing or packaging.
A dryer/cooler is the preferred equipment for high moisture products. However, care must be taken to ensure proper handling of the product. Like extrusion, drying/cooling needs to be optimized to ensure proper treatment and efficiency. One could over dry and start to burn the product or not dry enough. A trained operator will ensure correct operating parameters.