Plant Layouts
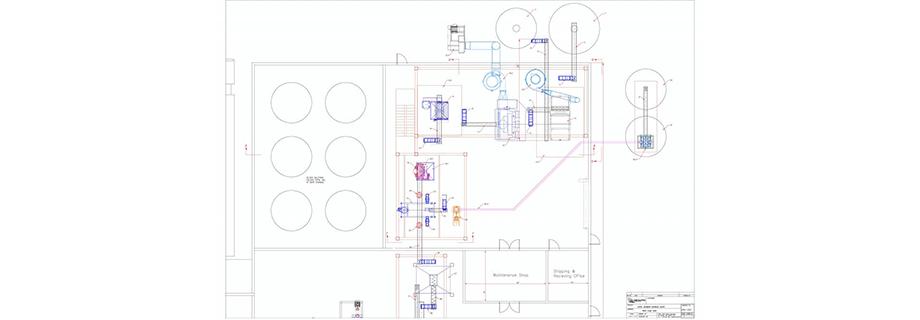
Here at Insta-Pro, we not only sell equipment, but we have the unique opportunity to provide engineering services as well. This can prove to be a valuable resource to help construct your new plant. While larger companies typically have resources for this already, most of our customers rely on this service to help establish product flow, equipment layouts, and project planning. Hopefully some of these ideas will help when planning your next project.
When we receive an inquiry, our customers generally already have an idea of what they want their plant to look like. The first step is to decide what they wish to produce and the scope of the project. Will this be a brand new building and process or will it go into an existing space? What capacity is it? Should there be room for future expansion? These are key questions needed to decide how best to lay out an efficient plant.
To start, a process flow chart shows how product moves within the plant. This gives an idea of equipment needs and production flow. This also serves as a guide to help with discussions and future equipment decisions. In the case of Insta-Pro, we have several vendors we work with and can offer equipment for everything inside the walls of the plant. Some customers prefer to work with their vendors, so this decision is important as well.
Flow diagrams help convey ideas about processes and capabilities. Their purpose is not to determine floor space requirements or final specifications, but act as a springboard to further enhance discussions. Drawings are simplified to represent the process, not what the equipment looks like and usually vary from company to company. They are useful for people new to the particular industry to help realize all of the steps involved in production and to get a sense of initial equipment needs.
Final Layouts
Flow diagrams are excellent tools for discussions, but once these initial questions get answers, it’s time to see what the actual plant will look like. The starting point is knowing if this is a new or existing building. Older buildings require a current floor plan to best place the equipment around any obstacles such as rooms and beams. This is the time to become detailed, so knowing actual or potential locations of items is key. Below is a partial list of things to considering when beginning the final layouts:
- Raw material storage
- Existing equipment/processes
- Receiving/unloading
- Final goods location
- Electrical locations
- Motor control room location
- Space to move equipment around during installation and maintenance
- Building heights, roofline layout
- Support structures (availability, location)
- Facility locations (offices, restrooms)
- Future expansion planning
This is only a partial list of things to consider, but these are important to remember. At Insta-Pro, we can go through several drafts before we have a completed, final layout ready for use. In this initial planning stage, several options can be presented to best fit the needs of the customer. Changes are much easier to do on the computer than in real life, so it’s a great opportunity to try many options to determine what works best. These initial drafts are constructed to scale and later ones are used during final installation. Correct heights, support structures, conveyors lengths and much more are determined from these layouts. Attention to detail and correct information are critical at this stage.
Regardless of who completes the layout, having a plan is essential. It is oftentimes said that “failing to plan is planning to fail” and without a direction, it’s likely there will be headaches and extra costs. Taking a little more time now to plan, will pay off in the end and could potentially save you money in the process.