Particle Size Reduction
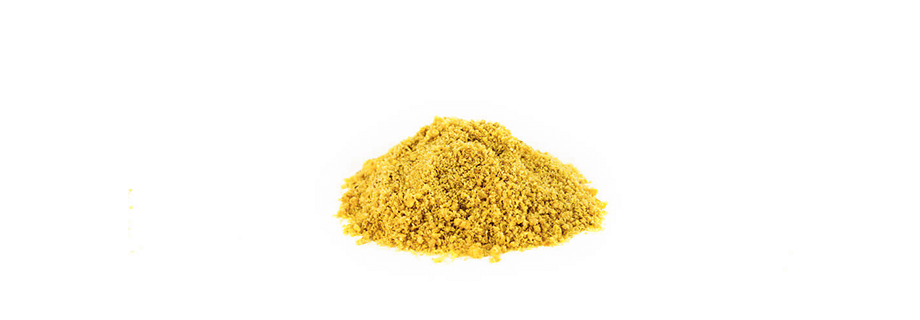
Regardless of your feed production process, there is a good chance that you will have to grind material to a suitable size for processing.
In the case of extrusion, there are multiple reasons for doing this. Smaller particles increase extruder efficiency by reducing the work it has to do. This leads to a better product and increased extruder life. Smaller particle sizes may also be needed for correct starch gelatinization and expansion of puffed products, reduction of anti-nutritional factors or so cutterhead dies do not clog during feed production. A smaller particle size also increases the feed efficiency for animals by increasing the available surface area and ability to obtain nutrients.
There are three main ways to reduce particle size in our industry. And they all have a purpose in food and feed processing. They are as follows:
Roller Mills
The design of the roller mill mimics the old methods of using round stones to crush seeds on a wheel. The modern interpretation of this uses two (or more) motor driven rollers to crush materials as they pass between the wheels. To help with cracking, these wheels can be shaped with different profiles to grab and crush. They can also turn at different speeds and be placed closer or farther together depending on the required grind size. Roller mills are ideal for simple cracking processes that do not require precise particle size distribution or fine grinds.
Hammer Mills
A very popular chose in the industry is the hammer mill. These are comprised of two major parts: the hammers and the screen. The hammers are free swinging and connected to a motor driven hub. The screen surrounds the hammers such that they do not hit the screen, but are very close. Product enters the hammer mill inside of the screen section where the spinning hammers are. The hammers break the materials and press them against the openings in the screen. This breaks and slices them to at least the size of the screen. The sized pieces pass through the bottom while any large particles remain until they are broken down small enough to pass through the screen. Hammer mills are ideal for most situations and can have narrow particle size distributions along with relatively fine grinds (down to ~1.5mm).
Pulverizers
Pulverizers are similar to hammer mills in terms of operation, but can grind down to very small particle sizes (0.150 mm or smaller). Instead of hammers and screens, pulverizers have vanes and mill plates. These require much higher horsepower compared to hammer mills but can grind material to fine flours which is difficult for hammer mills.
Step Grinding
An important consideration in particle size reduction is step grinding. Essentially, this is pre-grinding. The idea is to reduce the work of the machine by reducing the work it has to do on the product. In the case of pulverizers, it is highly recommended to do this for maximum efficiency. Initial investment costs may seem high, but decreasing overall power consumption and increasing productivity may be the beneficial result as some studies have shown a 6-12 month payback period. Other advantages include a more uniform product/distribution, higher grinding capacity and reduced equipment wear.
So, which one do you use?
The exact machine you will use will depend on your final product. Hammer mills are a good all-around choice but have limitations such as fine grind sizes. Roller mills and pulverizers are more specialized and recommending these will vary based on product as well (fish feed, dehulled beans, etc.). The best way to determine your requirements is to talk with industry leaders and those that have experience with this equipment.