Motor Starters
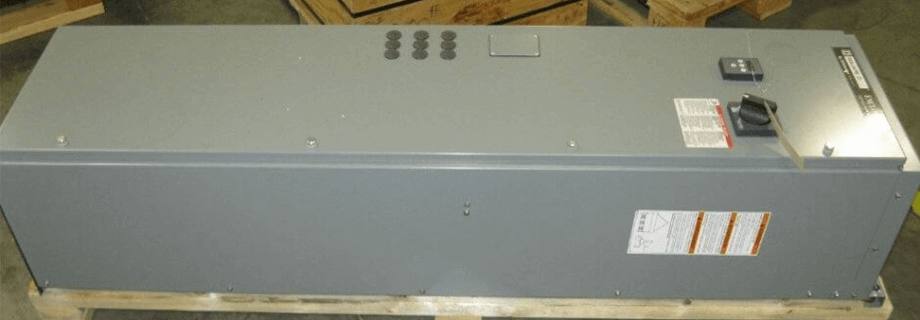
A simple, yet often overlooked item required in extrusion facilities are motor starters. This device is essentially a giant switch to supply power to a motor. Several companies offer these, but it’s important to understand their function so you can make the best decisions with your supplier. All motors will require some sort of starting device. The actual type will depend on the motor horsepower, the motor function, and what your local electrical company will allow for amperage load per device.
Types of starters
Across the line
These are the simplest form of starters. Much like a light switch, it connects and disconnects the power supply to the motor in either an “on” or “off” manner. This type of starter is limited to lower horsepower motors only. Typically, the highest horsepower motor allowed to use this type of starter is around 15-30 horsepower and is dependent on your local power supply company. The higher the horsepower, the higher the potential amperage draw. If you have a plant with many higher horsepower motors that start in this fashion, your amperage draw will be very high and you may get a call from the power company to explain yourself!
The main reason this method is limited is due to the amperage draw. Using this type of starter with our largest extruder that has a 350 horsepower motor would be a really bad idea. In fact, this was done at an early startup many years ago and shut down an entire town’s power supply! These larger horsepower motors require a special starter.
Soft starters (star/wye delta)
Larger motors require a gradual flow of power to them rather than all-at-once. For these, a soft starter is required. Like the name suggests, these starters regulate the power to the motor, so rather than sending all power to it at once, it controls the flow to slowly start the motor. This reduces the initial amperage draw into the system
Variable speed drives
Similar to a soft starter, variable speed drives offer another level of flexibility. These are able to control the frequency of the voltage going to the motor and thus, the speed the motor can run. We recommend these on some pressing applications in order to maximize the oil yield by slowing down the press RPMs. They are also required for feeder screws in which the rate of material must be adjusted to the corresponding flow rate. These offer more flexibility than a normal soft starter, but do cost more. Prices are coming down, so you will just have to compare your system needs to this pricing.
Non-reversing and reversing
An option on all starters is to have reversing or non-reversing capabilities. The starter can change the wiring such that the power is reversed, thus reversing the rotation of the motor. This is mainly used on screw conveyors so you can potentially remove blockages, but can be used on equipment as well. A good example is a hammer mill. A reversing starter can be used to even the wear within the mill by allowing it to turn clockwise for a while, then counter-clockwise to even out wear. Again, the use of this option will depend on your plant needs.
A qualified electrical vendor will be able to guide you to your best option. It is very helpful to have a basic understanding of your needs, however, as this will save them time specifying a correct system for your application. To help our customers, our equipment quotations will typically include soft starters for the extruder and oil press as they are generally the largest motors in the plant. Feel free to reach out to us if you have any questions.