Cooling Conveyors: A Simple Solution
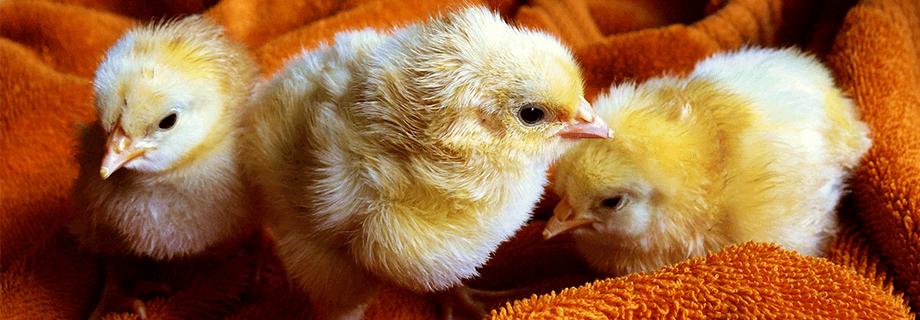
As the R&D Extrusion specialist, I like to cover subjects that are relevant to current extrusion operations. Oftentimes, we will be in contact with a number of customers who are experiencing similar situations in production. Lately we have heard from several customers who recently started using oil presses in their operations and are having problems with higher than normal oil residuals in their finished cake product. In every case, the issues have been traced back to how the extruded product is handled when going from the extruder to the oil press.
In the above-mentioned scenario, the problem exists likely because of excessive moisture in the product entering the oil press. Excessive moisture will cause the meal to slip in the press reducing amount of oil recovered. Things to look for as an indication that the meal going into the press is too high in moisture is as follows. Foam in the oil, or excessive fines coming out between the cage bars will indicate high moisture.
In order to stop the excessive moisture, the conveyor from the extruder to the oil press needs to be vented to allow for the removal of steam or moisture form the extruded product before it enters the press. For the oil press to get maximum efficiency, the product going in needs to be very dry (5% moisture). That is why we stress the use of lower moisture soybean in the process. The extruder will free up the moisture to be removed between the extruder and the press.
Typically you can remove about 50% of the moisture in the post-extruded soy by going through a cooler. The problem is that cooling the product before going to the press allows the oil to start binding back on to the meal, which also reduces the efficiency of the oil press.
The solution is to remove as much steam as possible without letting the meal cool too much. The best way to accomplish this is to use a cooling conveyor – a screw conveyor, typically a U-trough, with the top vented to allow the steam to escape.
It is also important to have a conveyor that is long enough to give the product enough time for the steam to leave. The shorter the distance between the extruder and oil press, the harder it is to get enough steam removed. If you do have a conveyor that covers only a short distance, a small fan can sometimes be used to move air across the top of the conveyor and remove the steam.
It seems so simple, but somewhere between the purchase of the equipment and the installation of the system, this part of the process sometimes gets forgotten or neglected. Although it is explained in the start-up process, it may often be overlooked because it may seem like a minor detail. When an issue comes up, it is often necessary to take a step back and look at some of the simpler operations to understand where the problem might be stemming from. The cooling conveyor can be seen as a simple part of the operation, but can have a big impact on the overall process. As always, Insta-Pro is just a phone call away, and we are always here to help your operations run smoothly.