TOM D WIP – L’ennemi du Lean Manufacturing
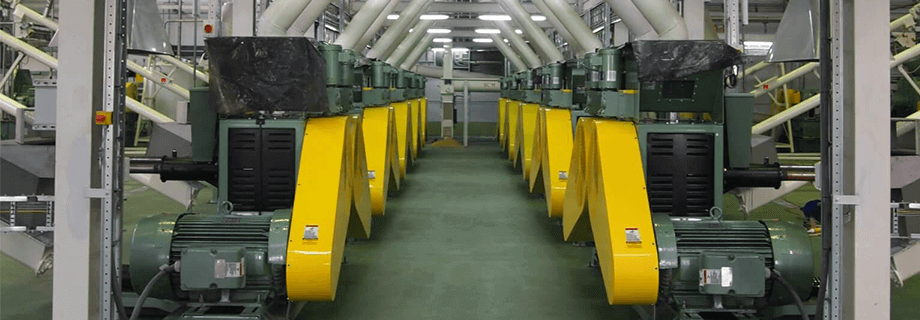
Le Lean Manufacturing (production sans gaspillages) est un concept qui existe depuis un certain temps, et qui est devenu le terme à la mode incontournable ces dernières années. Toute entreprise cherche à créer une culture « lean » basée sur le rendement, la productivité et un minimum d’erreurs. Qu’en est-il pour vous, dans votre propre usine ?
La référence pour la plupart des cultures lean est le système de production Toyota (ou TPS, pour « Toyota Production System »). Cette méthodologie est appliquée dans de nombreux environnements de production et peut être utilisée pratiquement n’importe où. L’un des points clés dans ce concept est la réduction des gaspillages, ce qui est désigné par le terme « Muda » dans le TPS. Tout processus peut être classé comme « à valeur ajoutée » ou « sans valeur ajoutée », et définir pour chaque processus à quelle catégorie il appartient permettra à votre exploitation d’être plus performante. Même s’il est vrai qu’éliminer les pertes permettra d’avoir un process plus efficace, par où commencer ? Voici une méthode simple d’analyse et d’évaluation pour chaque process.
Les 7 types de gaspillage
Il existe diverses phrases pour cela, mais si l’on prend la première lettre de chaque type de gaspillage (en anglais), on obtient : TOM D WIP. En évaluant chaque processus, on peut identifier les sources d’inefficacité et les éliminer. Chaque procédé devrait être évalué du point de vue de ce qu’il apporte, ou non, en matière de valeur ajoutée.
T – Transportation (transport)
Combien de fois le produit est-il transporté au cours du process ? Chaque fois qu’une chose est déplacée, le risque que celle-ci soit endommagée, perdue ou pire, augmente. Moins le produit est déplacé, mieux c’est. Prenons par exemple ce qui se passe après l’ensachage. Idéalement, après ensachage, le produit devrait être expédié. Tout passage par le stockage s’avère un risque d’endommager le produit.
O – Overproduction (surproduction)
La surproduction a tendance à occulter les problèmes. Des lots importants sont généralement utilisés afin de compenser le temps perdu avec des quantités excessives réalisées pour tenir compte des problèmes de production. Si un rappel a lieu, la taille du lot a désormais des chances d’être plus importante que ce qu’elle aurait dû être, et une quantité plus élevée de produit devra être éliminée. Autre inconvénient : un problème momentané peut survenir dans la production (mauvaise alimentation en matières premières, bourrage, etc.), et il se peut que cela ne soit pas détecté, du fait de la grande quantité de produit fabriquée avant que ce dernier n’arrive chez le client.
La surproduction diminue le niveau de contrôle sur le process et conduit le plus souvent à une autre forme de gaspillage : les stocks excédentaires. Un effet boule de neige peut se produire à partir de ce point : il vous faut à présent trouver de la place pour tout mettre, ce qui peut causer des retards et des déficiences potentielles parce qu’il y a des obstacles.
M – Motion (déplacements excessifs)
Quelle distance doit parcourir le produit pour sa transformation ? Si le processus suivant se trouve loin, il faut plus de temps pour que le produit y soit acheminé. De très grandes longueurs de convoyeur ou des distances excessives entre les machines sont des raisons possibles à cela. C’est la même chose pour les opérateurs. Par exemple, si un opérateur doit surveiller la cadence de production et manipuler en plus une machine d’emballage, les déplacements qu’il a à effectuer peuvent être excessifs. Peut-être qu’en répartissant différemment les charges de travail, ou encore en embauchant du personnel supplémentaire, il sera possible d’améliorer le rendement et de réduire les temps d’attente pour ce processus.
D – Defects (défauts)
Tout produit défectueux représente bien sûr un gaspillage. Une réduction des défauts entraîne systématiquement un meilleur rendement. Les défauts réclament soit un remaniement, soit une mise au rebut, et l’un comme l’autre font perdre du temps et ont un coût. Il se peut que des choses directement liées au process provoquent des défauts (par exemple une température trop élevée ou une manipulation inadaptée des granulés), mais ces derniers sont certainement provoqués à cause des gaspillages présentés ici. Si la production courante semble correcte mais que des problèmes subsistent, les déficiences peuvent être une conséquence d’autres gaspillages.
W – Waiting (attente)
Comme dit le proverbe, « le temps, c’est de l’argent ». Plus il faut de temps pour produire, plus on dépense d’argent, à cause des coûts d’exploitation. L’attente se produit lorsque le rythme de production n’est pas constant. Tout produit mis en attente avant d’être transformé prend de la place. Ce fait est généralement constaté dans les systèmes en fonctionnement discontinu (par lots). Une diminution des temps d’attente permet au process de se dérouler de façon plus régulière, dans la mesure où cela réduit les afflux soudains en production.
I – Inventory (stock)
Que se passe-t-il lorsque vous avez trop de produit ? Il est généralement inutile de stocker des quantités excessives de produits. Cela prend de la place et peut rendre les déplacements dans l’usine difficiles. L’espace de travail est précieux de nos jours ; mieux il est exploité, mieux c’est. Le stock doit être évalué et analysé, afin de s’assurer que ce qui est stocké ne l’est pas en dépit du bon sens. Avez-vous en réserve des pièces qui ne sont que très rarement utilisés ? Elles peuvent peut-être être déplacées pour gagner de la surface de production, ou de la place pour des choses plus souvent utilisées qui peuvent permettre de réagir plus vite vis-à-vis des clients.
P – Processing (traitement excessif)
Un traitement excessif implique d’en faire trop / d’ajouter des éléments inutiles. Pourquoi sécher un produit à 5 % d’humidité alors que 8 % est convenable ? Quelle nécessité d’avoir 13 vitamines alors que le client n’en demande que 11 ? Lors de l’évaluation d’un éventuel traitement excessif, il faut prendre en compte le rapport coût/avantages. Si sécher ou transformer en deçà d’un certain point est une garantie supplémentaire ou une stratégie marketing, le coût que cela représente doit être analysé par rapport aux coûts d’exploitation pour que ce soit justifié. Si ces méthodes sont appliquées pour compenser d’autres problèmes de production, résoudre d’autres formes de gaspillage sera probablement préférable.
Que puis-je faire ?
Aucun process n’est parfait, mais l’idée fondamentale d’amélioration continue devrait toujours être présente. On trouve toujours des manières de s’améliorer et de devenir plus efficace. Un manière valable de se lancer consiste à mettre par écrit sur une fiche chaque étape du process dans le détail, y compris la durée de cycle, en utilisant une fiche par processus. En fonction de la taille de votre usine, vous pourriez avoir besoin d’un certain nombre de fiches ! En utilisant des fiches, vous profitez d’un moyen visuel de comprendre s’il existe des gaspillages dans le système. Vous pouvez alors réorganiser les étapes de transformation ou les évaluer pour déterminer si elles sont nécessaires ou pas. Au final, vous pourriez réaliser que vous pouvez être plus rentable sans dépenser un centime.